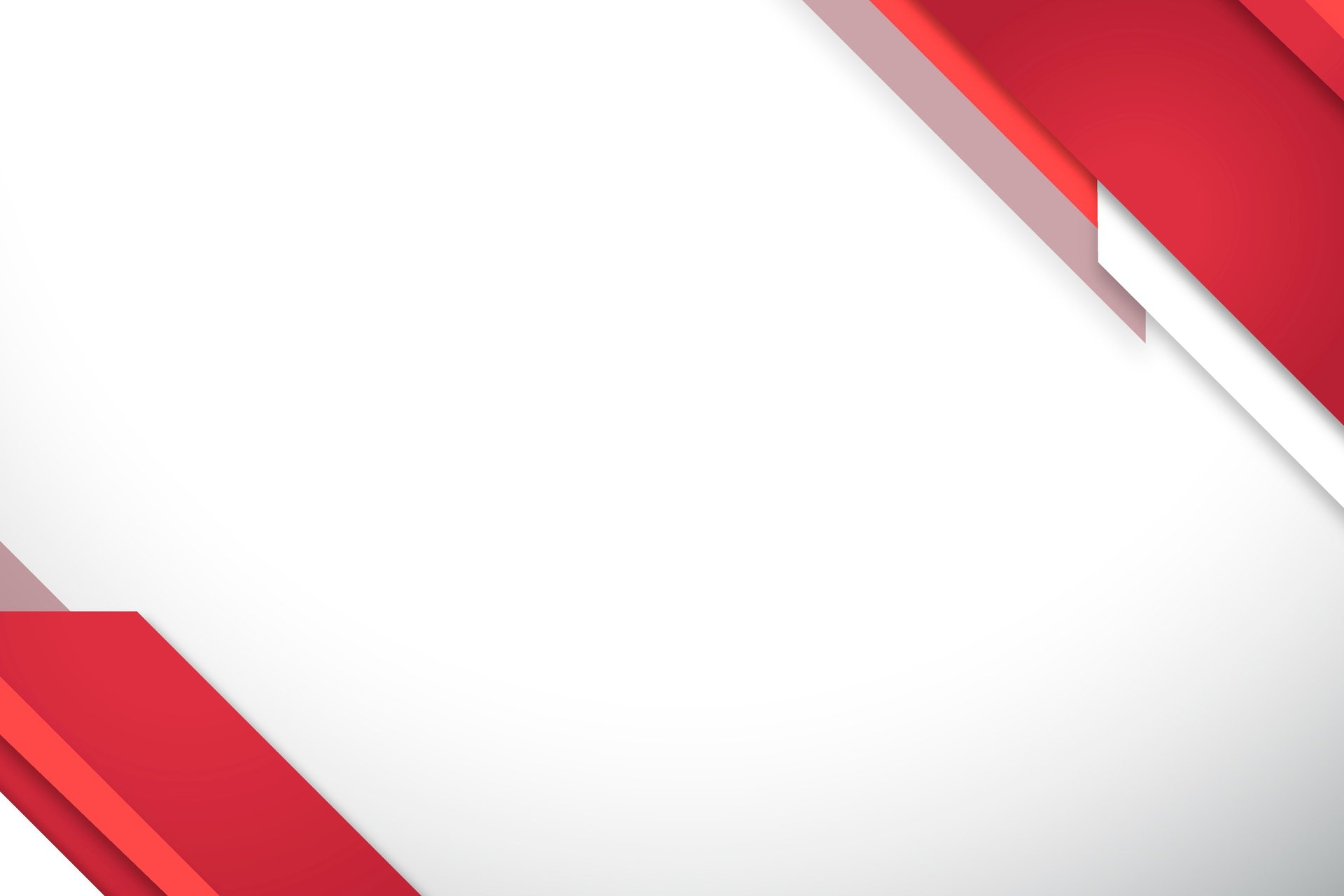
Introduction to the production process and advantages of rock wool board
6/13/20245 min read

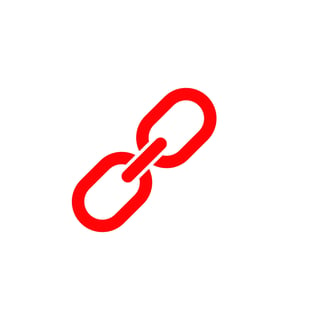














Rock wool board is a fiber material formed by softening naturally formed ores. Its process flow roughly includes 8 steps, as follows:
Categories
Popular
Applications of Glass Wool Board:
Interior Wall Compartments:
Enhances the functionality and aesthetics of interior spaces.
Ceiling Systems:
Provides effective insulation for ceilings, contributing to energy efficiency.
Insulation of Iron Sheet Air Ducts or Bellows:
Ideal for insulating ductwork, ensuring thermal efficiency.
Sound Absorption and Noise Reduction:
Reduces noise levels in machine rooms, creating a quieter working environment.
Exterior Wall Insulation:
Offers insulation for residential building exteriors, contributing to energy savings.
Glass Wool Insulation

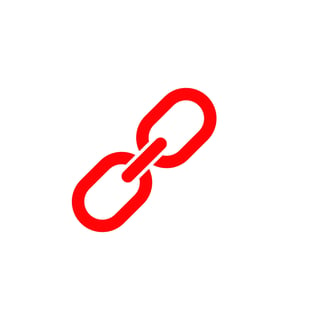

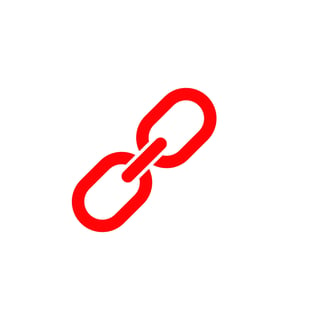

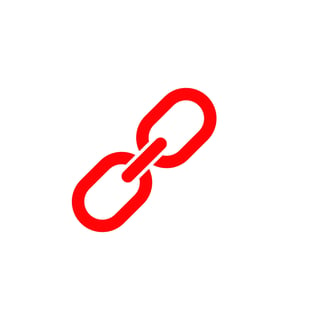

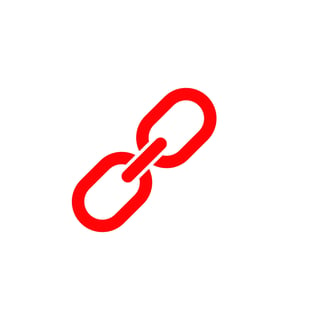

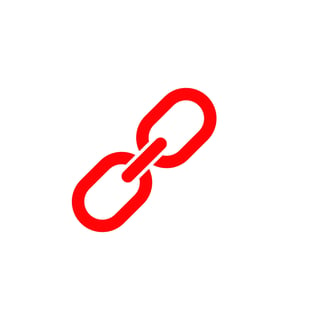
Rock wool board is a fiber material formed by softening naturally formed ores. Its process flow roughly includes 8 steps, as follows:
Firstly, the slag of basalt should be placed in a high melting furnace for melting. After the basalt is melted, it can change the physical structure of the natural ore and initially form the structure of a rock wool board.
Secondly, high-speed centrifugal spinning should be performed on the melted material. After the slag of basalt is melted at high temperatures, it will become a relatively soft state. At this time, high-speed centrifugal equipment is used for treatment, and the softened material will slowly form a silk thread state. Then, through rotation, all the centrifuged silk will slowly stick together, and after being stuck together, it will be processed by a special process to form rock wool cotton.
Thirdly, a high-speed blower should be used to cool the completed inorganic cotton to the desired shape. Because the newly produced inorganic cotton is in an unstable form, we use a high-speed blower to lower the material temperature and make it easier to form.
Fourthly, carry out process treatment. We need to add products with water increasing and bonding properties to inorganic cotton, making it impervious to moisture and increasing its strength and hardness.
Fifthly, use highly efficient adhesive materials to spray inorganic cotton. After shaping the inorganic cotton, we need to spray some high-efficiency adhesive on its surface to make its shape more stable.
Sixth, use the pendulum method to continuously increase the compression force of inorganic cotton, increase its density and hardness.
Seventh, use high temperature for drying treatment. We need to use high temperature to dry high-density materials and let all the moisture inside dry.
Eighth, by cutting the already prepared materials into different sizes of rock wool boards, we can obtain the rock wool board with insulation function that we use.
What are the characteristics and advantages of rock wool board? Below is a detailed introduction:
Stable performance: Rock wool board is made of high-quality basalt as the raw material, which has a unique structure that prevents performance from changing with the environment, making its performance more stable. Even after more than ten years of use, it will not change in shape or other aspects.
Thermal insulation: Rock wool board has the characteristics of good thermal insulation and can be used in scenarios such as building construction, which can play a role in building thermal insulation and obtain a more suitable living environment.
Noise reduction and sound insulation: The composition of rock wool board can isolate noise, creating a quieter environment.
Hydrophobic water absorption: This material has a certain water absorption ability and also has the ability to repel water. Rock wool boards can be used to solve problems such as water conservation or water repellency.
Green and environmentally friendly: The raw materials used are natural ores, making the production and use process even more environmentally friendly.
Shenzhou Energy Saving Technology Group Co., Ltd. is an energy saving and environmental protection enterprise integrating research and development, manufacturing and service of thermal insulation and sound absorption and noise reduction materials. The Group has six subsidiaries and ten industrial parks, producing five main series of products of rubber foam, glass wool, ceramic wool, sound absorption and noise reduction materials, and rock wool. Its products are widely used in construction, central air conditioning, refrigerator refrigeration, petrochemical, Marine locomotive, aerospace, thermal power, sound-absorbing noise reduction, and other industries.
After more than 40 years of exploration and sharpening, Shenzhou Group has become a leading manufacturer in the heat insulation and energy saving industry . The group covers an area of 1.06 million square meters, including a construction area of 680,000 square meters. Euipped with internationally advanced production equipment and technology, Shenzhou’s annual production volume of rubber foam is 2.6 million m³, glass wool 230,000 tons, rock wool 120,000 tons, and ceramic wool 28,000 tons. While solving the employment issue of more than 2,000 people, Shenzhou also created considerable economic and social benefits.

Why Choose SHENZHOU Glass Wool Board?
SHENZHOU® Glass Wool Board not only meets the essential requirements of thermal insulation but also excels in sound absorption and noise reduction. Its adaptability to various settings, coupled with the convenience of construction and installation, positions it as a leading choice for architects, builders, and contractors.
In conclusion, the broad application prospects of SHENZHOU® Glass Wool Board make it a comprehensive solution for enhancing comfort, energy efficiency, and acoustic performance across diverse projects. Choose SHENZHOU® for insulation solutions that go beyond expectations.
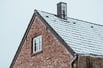
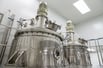
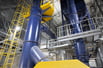
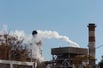
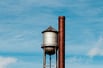
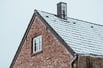
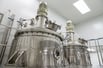
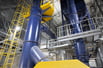
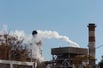
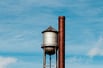
About Us
Click the button below to get more information about us
Newsletter
Click to subscribe for more information
Follow Us
Contact Us
Address
Dacheng town, Langfang City, Hebei province, China
Phone
+86 185 03165 626