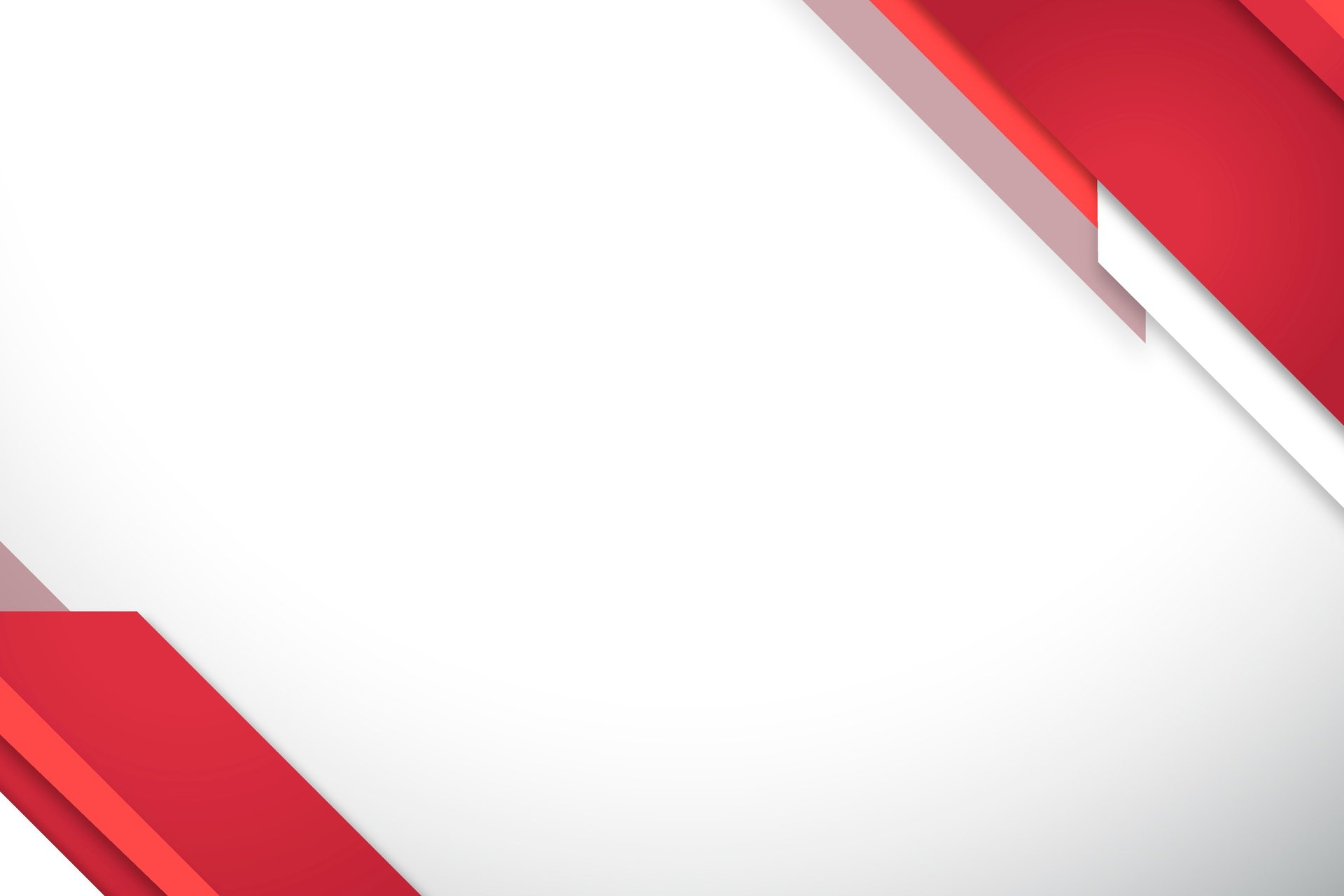
How do you make rock wool?
7/8/20246 min read

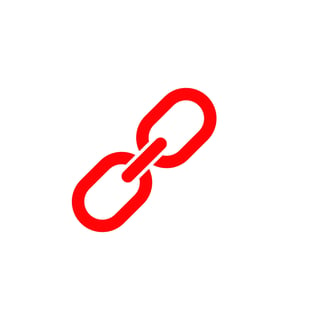














Making rock wool is a complex process that involves multiple steps. It mainly uses volcanic rock (or similar high silicon materials) to melt at high temperatures, and then converts it into fine rock wool fibers through special spinning techniques. These fibers are then collected and processed into various shapes and sizes of rock wool products, such as insulation boards, sound insulation boards, etc. The following are the detailed steps of the rock wool production process:
1、 Raw material preparation
The main raw materials for rock wool are volcanic rocks (such as basalt) or similar natural ores. These ores are crushed, ground, and screened to obtain raw material particles that meet the requirements. These particles need to have high silicon content and low impurity content to ensure the quality and performance of rock wool.
2、 Melting
Send the prepared raw material particles into the furnace and melt them at high temperatures (usually exceeding 1500 ° C). During this process, silicon, aluminum, and other metallic elements in the raw materials undergo chemical reactions, forming a viscous melt. This process requires precise control of temperature and time to ensure the quality and stability of the melt.
3、 Spinning
The melted melt is fed into a spinning machine and stretched into fine rock wool fibers through a high-speed rotating centrifugal wheel. There is a high-speed rotating centrifugal wheel inside the spinning machine, and the melt is thrown out under the action of the centrifugal wheel, forming fibrous substances. These fibers gradually solidify during the cooling process, forming rock wool fibers with certain strength and toughness.
Categories
Popular
Applications of Glass Wool Board:
Interior Wall Compartments:
Enhances the functionality and aesthetics of interior spaces.
Ceiling Systems:
Provides effective insulation for ceilings, contributing to energy efficiency.
Insulation of Iron Sheet Air Ducts or Bellows:
Ideal for insulating ductwork, ensuring thermal efficiency.
Sound Absorption and Noise Reduction:
Reduces noise levels in machine rooms, creating a quieter working environment.
Exterior Wall Insulation:
Offers insulation for residential building exteriors, contributing to energy savings.
Glass Wool Insulation

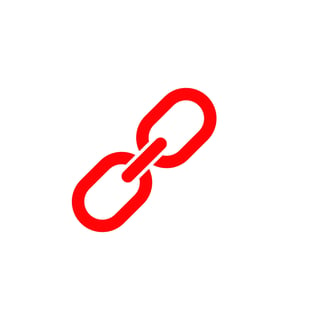

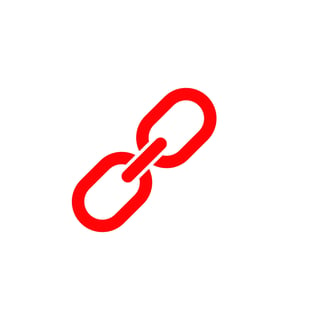

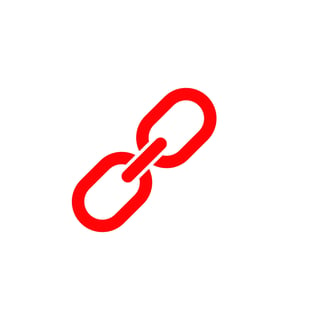

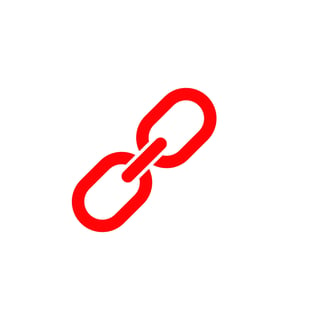

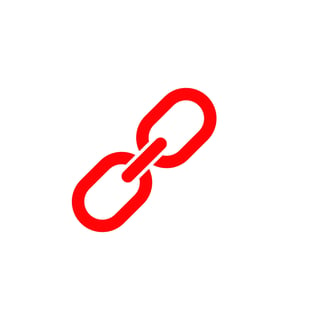
4、 Collection and processing
The spun rock wool fibers are transported to the collection area through conveyor belts or airflow. In this area, fibers are evenly distributed and attached to a moving mesh belt. As the mesh moves, fibers gradually accumulate and form a uniform layer of rock wool. Next, this layer of rock wool undergoes processing steps such as cutting, compression, and solidification to form rock wool products of different shapes and sizes.
5、 Post processing
The rock wool products made need to go through a series of post-processing steps to improve their performance and service life. These post-processing steps include surface treatment, waterproof treatment, fire prevention treatment, etc. Among them, surface treatment mainly involves polishing and cleaning rock wool products to remove impurities and uneven parts on the surface; Waterproof treatment involves coating a layer of waterproof agent on the surface of rock wool products to prevent water infiltration; Fire prevention treatment is to improve the fire resistance of rock wool products by adding flame retardants and other methods.
6、 Quality control and testing
Quality control and testing are crucial steps in the production process of rock wool. By conducting strict testing and evaluation of raw materials, melts, fibers, and finished products, it is possible to ensure that the quality and performance of rock wool products meet relevant standards and requirements. These testing items include chemical composition analysis, physical performance testing (such as density, strength, thermal conductivity, etc.), environmental performance evaluation, etc.
7、 Environmental Protection and Sustainable Development
As an environmentally friendly building material, rock wool also pays attention to environmental protection and sustainable development in its production process. In terms of raw material selection, priority should be given to natural ores with good environmental performance; Using energy-saving technologies and equipment during melting and spinning processes; In the post-processing stage, use environmentally friendly materials and additives; At the same time, strengthen waste treatment and resource recycling to reduce environmental pollution and resource waste in the production process.
8、 Application Fields and Prospects
Rock wool, as an excellent material for insulation, sound insulation, and fire prevention, is widely used in fields such as construction, transportation, and industry. With the increasing emphasis on environmental protection and energy conservation, the market demand for rock wool is also increasing. In the future, rock wool production technology will continue to develop and innovate, further improving the performance and quality of products; At the same time, strengthen the research and development of composite applications with other materials, and expand the application fields and market prospects of rock wool.
Shenzhou Energy Saving Technology Group Co., Ltd. is an energy saving and environmental protection enterprise integrating research and development, manufacturing and service of thermal insulation and sound absorption and noise reduction materials. The Group has six subsidiaries and ten industrial parks, producing five main series of products of rubber foam, glass wool, ceramic wool, sound absorption and noise reduction materials, and rock wool. Its products are widely used in construction, central air conditioning, refrigerator refrigeration, petrochemical, Marine locomotive, aerospace, thermal power, sound-absorbing noise reduction, and other industries.
After more than 40 years of exploration and sharpening, Shenzhou Group has become a leading manufacturer in the heat insulation and energy saving industry . The group covers an area of 1.06 million square meters, including a construction area of 680,000 square meters. Euipped with internationally advanced production equipment and technology, Shenzhou’s annual production volume of rubber foam is 2.6 million m³, glass wool 230,000 tons, rock wool 120,000 tons, and ceramic wool 28,000 tons. While solving the employment issue of more than 2,000 people, Shenzhou also created considerable economic and social benefits.

Why Choose SHENZHOU Glass Wool Board?
SHENZHOU® Glass Wool Board not only meets the essential requirements of thermal insulation but also excels in sound absorption and noise reduction. Its adaptability to various settings, coupled with the convenience of construction and installation, positions it as a leading choice for architects, builders, and contractors.
In conclusion, the broad application prospects of SHENZHOU® Glass Wool Board make it a comprehensive solution for enhancing comfort, energy efficiency, and acoustic performance across diverse projects. Choose SHENZHOU® for insulation solutions that go beyond expectations.
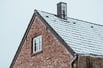
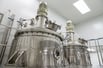
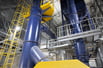
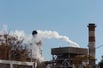
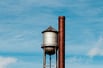
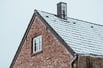
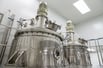
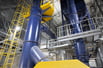
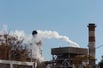
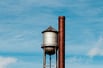
About Us
Click the button below to get more information about us
Newsletter
Click to subscribe for more information
Follow Us
Contact Us
Address
Dacheng town, Langfang City, Hebei province, China
Phone
+86 185 03165 626