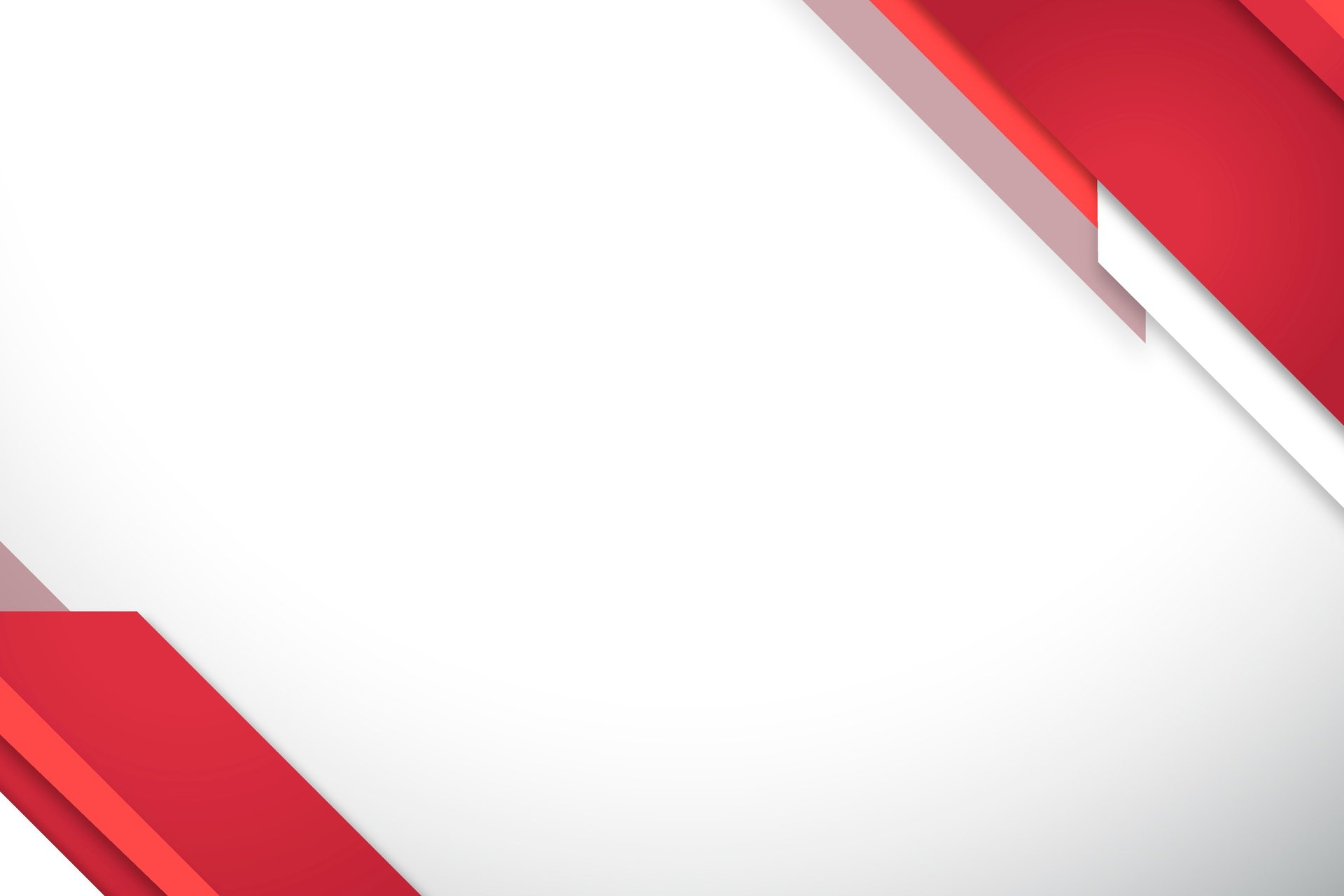
Comprehensive explanation of the production process of glass wool roll felt
6/4/20245 min read

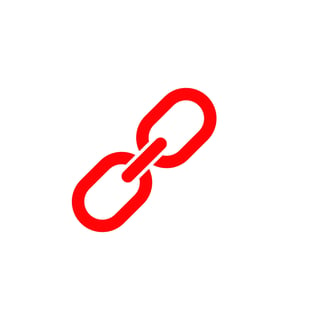














Glass wool felt, as a high-quality insulation material, is widely used in fields such as construction, chemical engineering, and power. Its production process is rigorous and complex. Below, we will comprehensively explain the production process of glass wool roll felt, so that readers can better understand this product.
Categories
Popular
Applications of Glass Wool Board:
Interior Wall Compartments:
Enhances the functionality and aesthetics of interior spaces.
Ceiling Systems:
Provides effective insulation for ceilings, contributing to energy efficiency.
Insulation of Iron Sheet Air Ducts or Bellows:
Ideal for insulating ductwork, ensuring thermal efficiency.
Sound Absorption and Noise Reduction:
Reduces noise levels in machine rooms, creating a quieter working environment.
Exterior Wall Insulation:
Offers insulation for residential building exteriors, contributing to energy savings.
Glass Wool Insulation

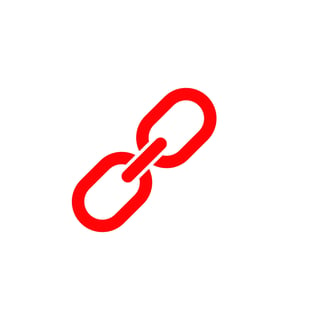

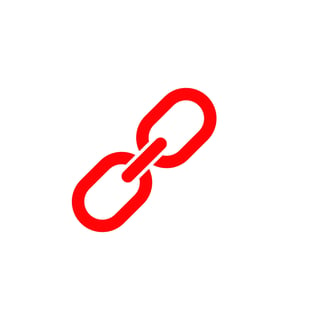

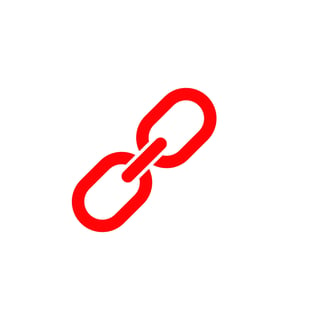

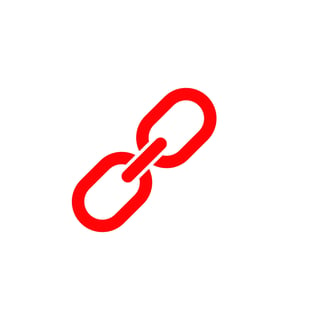

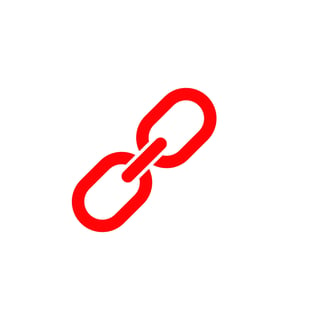
Firstly, the preparation of raw materials is the first step in the production of glass wool felt rolls. The main raw materials include natural ores such as quartz sand, dolomite, wax stone, as well as chemical raw materials such as soda ash and boric acid. These raw materials need to undergo strict screening and proportioning to ensure the quality and performance of the final product. During the preparation process, the raw materials need to be crushed, ground, and mixed for the subsequent melting process.
The next step is the melting process. Put the prepared raw materials into the furnace, and after high-temperature heating, the raw materials gradually melt to form liquid glass. During the melting process, strict control of temperature and time is required to ensure the quality and uniformity of liquid glass. At the same time, the atmosphere inside the furnace also needs to be controlled to avoid the generation of impurities and bubbles.
After melting, the liquid glass needs to undergo fibrosis treatment. This process is usually carried out using centrifugal injection or flame method. The centrifugal spraying method is to use a high-speed rotating centrifuge to shake liquid glass into fibers, while the flame law uses high-temperature flames to blow liquid glass into fibers. Both methods have their own advantages and disadvantages. The centrifugal injection method has high production efficiency and uniform fiber quality, while the flame method can produce finer fibers.
The fiberglass after fibrosis treatment needs to be collected and shaped. During the collection process, fibers are transported to the molding machine through conveyor belts or airflow. In the molding machine, fibers are evenly distributed on the conveyor belt and a glass wool layer with a certain thickness and density is formed through processes such as roller pressing and needle punching. Next, roll the glass wool layer to form a felt like product.
After the roll felt is formed, a series of post-treatment processes are also required. The first step is curing treatment, which stabilizes the fiber structure of the glass wool felt through heating or chemical methods. Next is surface treatment, which can spray waterproof and fireproof agents on the surface of the felt to improve its waterproof and fireproof properties. In addition, cutting, packaging and other processes can also be carried out as required for transportation and use.
Quality control is a crucial part of the entire production process. Manufacturers need to establish strict quality management systems and conduct strict inspections and tests on raw materials, semi-finished products, and finished products. This includes testing the chemical composition, particle size and other indicators of raw materials, monitoring the temperature, viscosity and other parameters of liquid glass, and testing the density, thermal conductivity and other properties of finished products. Only by ensuring that every step meets quality requirements can high-quality glass wool felt products be produced.
In addition, with the continuous progress of technology, the production process of glass wool felt is also constantly innovating and improving. For example, some advanced manufacturers have adopted automated and intelligent production lines, achieving precise control of the production process through computer control systems. This not only improves production efficiency, but also reduces energy consumption and environmental pollution.
Overall, the production process of glass wool felt is a complex and delicate process that requires strict control over raw materials, processes, and quality. Through continuous technological innovation and improvement, manufacturers can produce higher quality and efficient glass wool felt products, providing strong support for the development of construction, chemical, power and other fields.

Why Choose SHENZHOU Glass Wool Board?
SHENZHOU® Glass Wool Board not only meets the essential requirements of thermal insulation but also excels in sound absorption and noise reduction. Its adaptability to various settings, coupled with the convenience of construction and installation, positions it as a leading choice for architects, builders, and contractors.
In conclusion, the broad application prospects of SHENZHOU® Glass Wool Board make it a comprehensive solution for enhancing comfort, energy efficiency, and acoustic performance across diverse projects. Choose SHENZHOU® for insulation solutions that go beyond expectations.
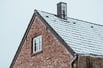
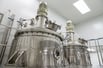
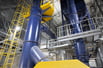
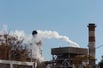
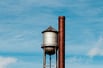
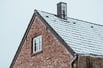
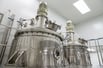
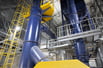
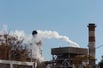
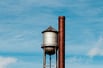
About Us
Click the button below to get more information about us
Newsletter
Click to subscribe for more information
Follow Us
Contact Us
Address
Dacheng town, Langfang City, Hebei province, China
Phone
+86 185 03165 626